What is FLOEFD?
In engineering and design, getting a comprehensive understanding of fluid flow behavior can help you optimize product performance and drive innovation.
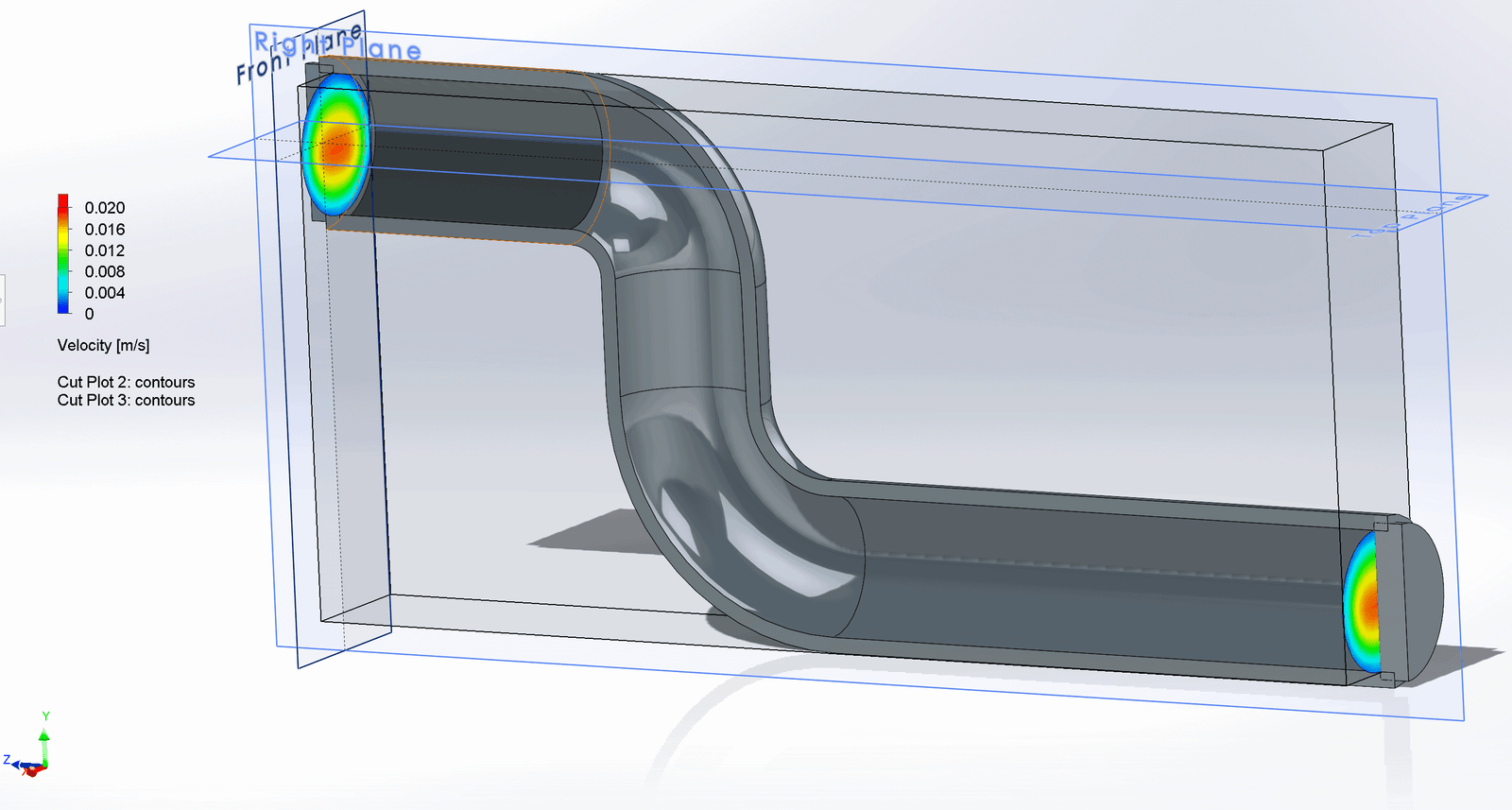
What is FLO EFD in Computation Fluid Dynamics (CFD)?
In engineering and design, getting a comprehensive understanding of fluid flow behavior can help you optimize product performance and drive innovation.
To meet this need, Mentor, a Siemens Business, created FLOEFD – a cutting-edge computational fluid dynamics (CFD) software that seamlessly integrates within your favorite Computer-Aided Design (CAD) environment.
Imagine being able to perform fluid flow and heat transfer simulations directly within your CAD software, without needing time-consuming data translation or transferring between different tools. FLOEFD makes this a reality, giving engineers a user-friendly and intuitive CFD solution right at their fingertips.
Volupes contacts for Simcenter FLOEFD
FLOEFD CFD simulation enhances the design process, right from the start
With FLOEFD, design engineers can explore a wide range of simulations, including steady-state and transient fluid flow analysis, heat transfer analysis, multiphase flow analysis, turbulence modeling, and more. This powerful tool helps you gain valuable insights into the behavior of fluids within your designs, empowering you to optimize performance, identify potential issues, and make informed design decisions early on.
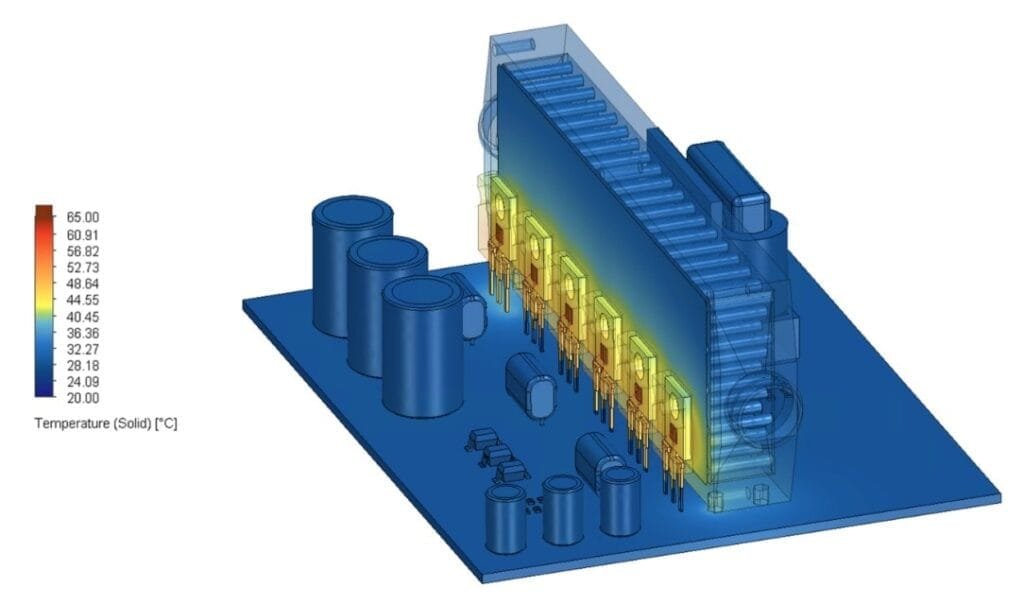
Access anything design engineers build with CAD geometry, directly
One of the standout features of FLOEFD is its seamless CAD integration. Whether you work with Siemens NX, PTC Creo, CATIA V5, Solid Edge, or SolidWorks, FlOEFD integrates with your preferred CAD system. This takes away the need for tedious data translation, ensuring that any changes made to your CAD model are automatically reflected in the CFD simulation. Real-time design updates create a streamlined workflow, allowing you to iterate and refine your designs with ease.
Beyond CAD geometry
FLOEFD goes beyond CAD integration to offer intelligent automation capabilities. The software provides robust automated meshing technology, simplifying the simulation setup process and saving you time that can be spent on other pressing tasks. By automating these essential steps, FLOEFD empowers engineers of all skill levels to leverage the power of CFD simulations, regardless of their expertise in traditional CFD tools.
By utilizing FLOEFD, you can transform your design process, reduce reliance on physical prototyping, and get products to market faster. With the ability to analyze fluid flow behavior directly within your CAD environment. Make informed decisions early in the design cycle, optimizing products for performance, efficiency, and reliability.
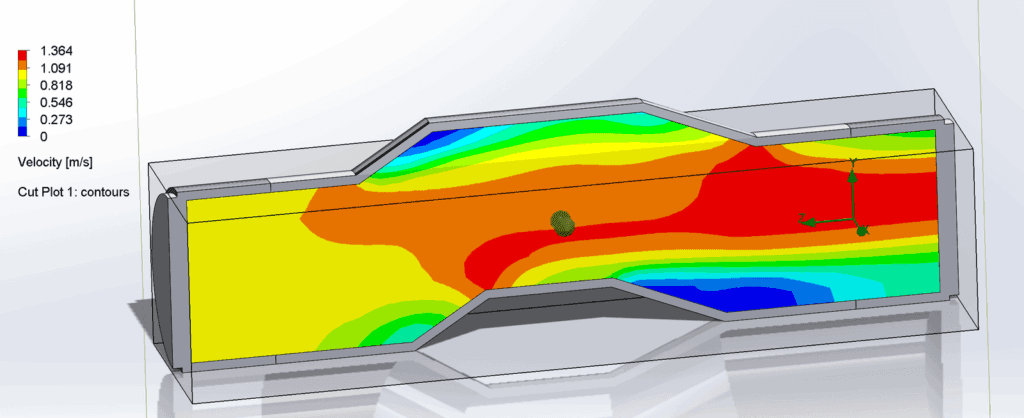
Solve fluid flow and heat transfer problems
Whether you need to predict temperature distribution, pressure drop, or fluid behavior, FLOEFD offers a wide range of capabilities to simulate and understand complex heat and fluid flow phenomena.
With intelligent automation features, like automatic mesh refinement and real-time design updates, engineers can efficiently explore multiple design iterations, identify issues early on, and make informed choices to optimize product performance and reliability. Simcenter FLOEFD empowers engineers to confidently tackle heat and fluid flow challenges, saving time, reducing costs, and creating better designs.
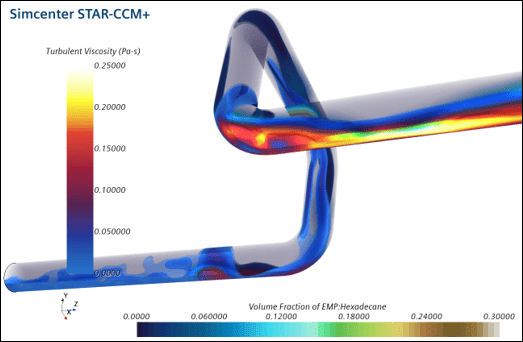
CAD-embedded computational fluid dynamics simulation
CAD-embedded CFD simulation with Simcenter FLOEFD revolutionizes the way engineers approach fluid dynamics analysis. By seamlessly integrating into popular CAD software, it enables engineers to perform CFD simulations directly in their familiar design environment.
With CAD-embedded CFD, there’s no need for data translation or transferring between different tools, streamlining the workflow and saving time. Engineers can quickly and efficiently analyze fluid flow simulation data behavior, heat transfer, and other critical parameters to obtain optimized product performance.
The real-time design updates ensure that any modifications made in the CAD model are immediately reflected in the CFD simulation, facilitating rapid iteration and design refinement. Make informed decisions, enhance collaboration, and accelerate the product development process.
A straight line from geometry to CFD
The straight line from geometry to CFD with Simcenter FLOEFD represents a paradigm shift in the world of engineering. Traditionally, the design process of transitioning from geometry creation to accurate computational fluid dynamics (CFD) analysis involved complex and time-consuming steps. However, with FLOEFD, engineers can now bridge the gap between geometry and CFD simulations.
Reduce time-to-solution by up to 75%
Intelligent automation: FLOEFD incorporates intelligent automation features, such as automated meshing. Generating high-quality meshes is a time-consuming task in traditional CFD simulations, but FLOEFD automates this process, reducing the manual effort from design engineers, and overall simulation time.
Real-time design updates: With FLOEFD, any modifications made to the CAD geometry are instantly reflected in the CFD simulation. Real-time design updates eliminate the need to start the simulation setup from scratch whenever design changes happen, saving a lot of time and enabling quick design iteration.
Interactive analysis and visualization: FLOEFD serves as an interactive analysis tool with data visualization, that helps engineers to quickly assess and understand the simulation results.
Real-time visualization of flow patterns, temperature distribution, and other parameters allows for faster identification of design issues or opportunities for improvement.
Robust solver technology: FLOEFD uses powerful and efficient solver technology that delivers fast and accurate results. This helps engineers obtain the simulation outputs they need in a shorter time frame, reducing the overall time to solution.
It also enables frontloading CFD processes by moving CFD simulation early into the process. As a result, engineers can iterate through design variations rapidly, optimize their designs more efficiently, and make informed decisions in a shorter time span. Ultimately, this time-saving advantage allows engineers to accelerate product development cycles, reduce time to market, and stay ahead in a competitive landscape.
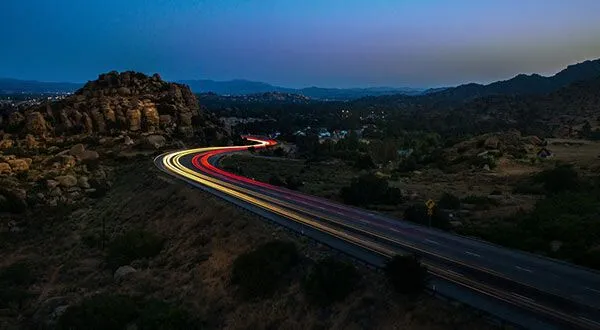
Featured success stories
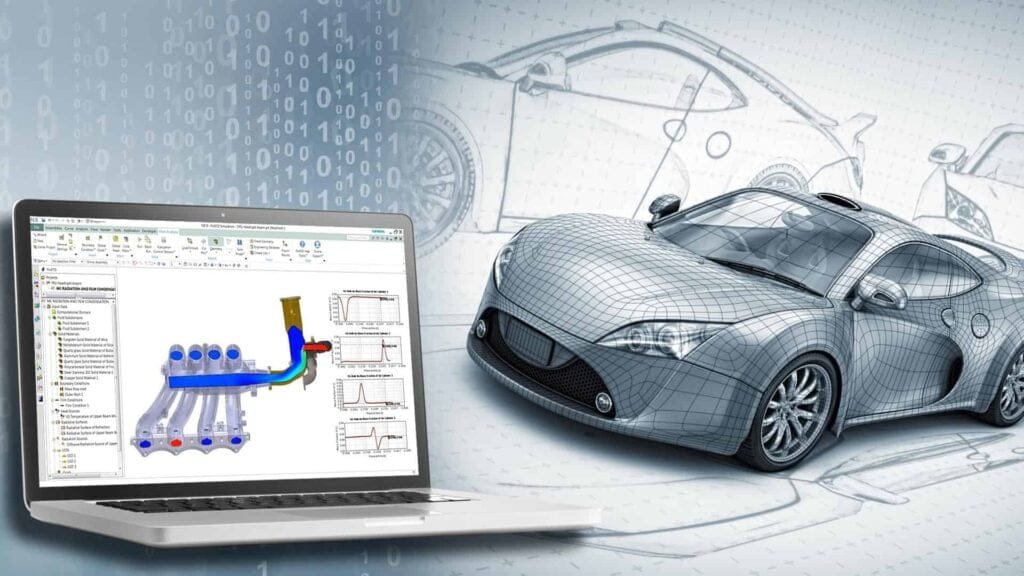
Don’t miss out on the latest updates
Subscribe to Volupe newsletter today and take your engineering and simulations skills to the next level.
In-depth analysis tools
With FLOEFD, engineers gain access to an array of advanced analysis capabilities, including steady-state and transient fluid flow analysis, heat transfer analysis, turbulence modeling, multiphase flow analysis, natural convection analysis, and conjugate heat transfer.
These tools enable engineers to delve deep into the intricate fluid behavior within their designs, offering valuable insights and helping optimize product performance.
Concurrent CFD analysis is a game-changer that FLOEFD brings to the table. Engineers can now perform multiple CFD simulations at the same time, allowing them to efficiently compare and evaluate different design options. This concurrent analysis capability speeds up the design exploration process and empowers engineers to make data-driven decisions based on comprehensive and timely information.
FLOEFD’s in-depth analysis tools not only provide accurate results but also ensure an intuitive user experience. The software seamlessly integrates within popular CAD platforms, eliminating the need for data transfer or complex setup procedures. Engineers can leverage the familiar CAD environment to perform detailed CFD analysis, saving time and effort.
With Simcenter FLOEFD, engineers can conduct in-depth analysis and leverage the power of concurrent CFD analysis to explore design options efficiently. The software’s comprehensive features, intuitive interface, and seamless CAD integration empower engineers to optimize product designs, enhance performance, and drive innovation in their respective fields (think everything from manufacturing to cosntruction, automotion and space exploration). Experience the depth of analysis offered by Simcenter FLOEFD and unlock the full potential of CFD simulations.
Automate to innovate
If analysis, automatic recognition, and identifying and recognizing various components and features within a CAD model are important to your work, Simcenter FLOEFD can revolutionize your design process with automation. This feature streamlines the setup process by automatically detecting and assigning appropriate boundary conditions, material properties, and physics settings to the recognized components. Overall, Simcenter FLOEFD projects are more effective and make quicker work of tasks that can be performed by machines.