What is FLOTHERM?
It’s no secret that managing heat effectively is crucial in various fields, including electronics and industrial machinery. This is part of why Siemens designed FLOTHERM, an advanced software tool that helps engineers tackle complex thermal problems and optimize designs for efficient heat management.
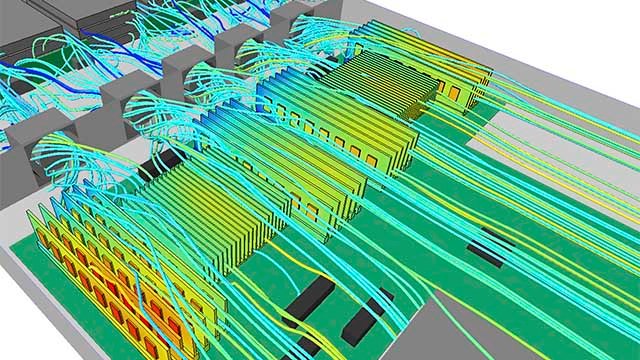
What is FLOTHERM - Thermal Analysis Software by Siemens EDA | DirectIndustry
It’s no secret that managing heat effectively is crucial in various fields, including electronics and industrial machinery. This is part of why Siemens designed FLOTHERM, an advanced software tool that helps engineers tackle complex thermal problems and optimize designs for efficient heat management.
With FlOTHERM, engineers have powerful capabilities at their disposal to address the complications and hazards that come with thermal issues in different industries. This software combines Computational Fluid Dynamics (CFD) with robust thermal analysis to provide a complete understanding of heat transfer and fluid flow phenomena.
Beat the heat
Efficient heat transfer is an engineer’s best weapon against excessive temperatures, which can lead to performance degradation, component failures, and increased costs. From chips to boards to fully electronic systems, a number of factors play a role in effective heat control.
The challenges that come from tackling heat transfer issues include everything from complex geometries to varying thermal loads and the need for precise predictions. This is where Simcenter FLOTHERM comes to the rescue.
With its advanced capabilities and intuitive interface, FLOTHERM empowers mechanical design engineers to create virtual models and simulate, analyze, and optimize heat transfer in a wide range of applications, from electronics cooling to industrial systems.
Some of our Simcenter clients
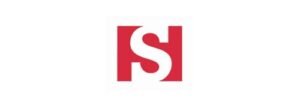
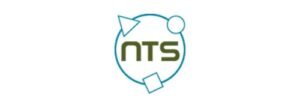
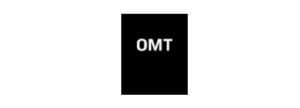
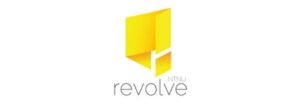
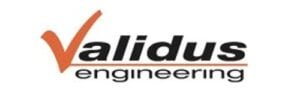
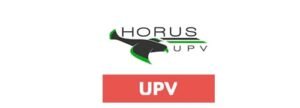
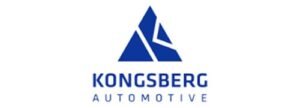
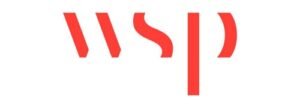
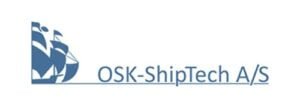
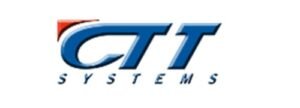
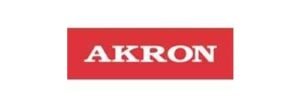
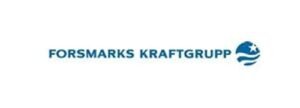
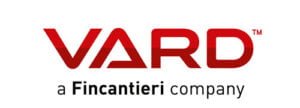
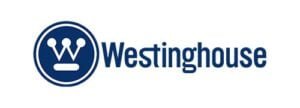
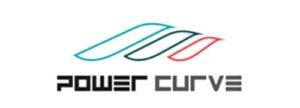
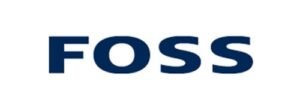
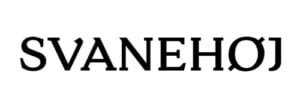
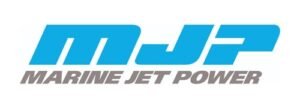
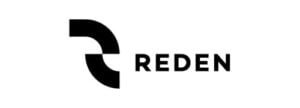
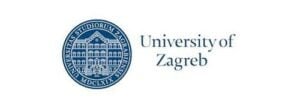
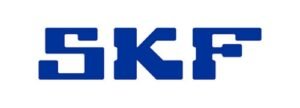
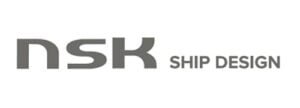
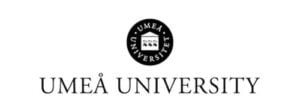
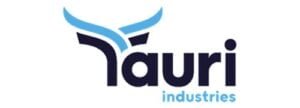
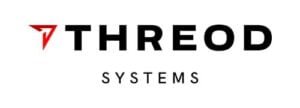
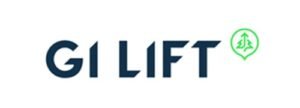
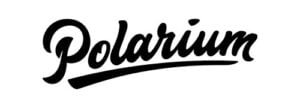
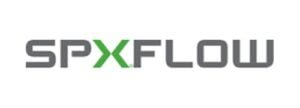
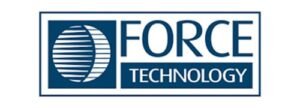
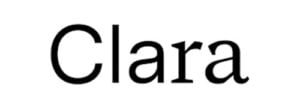
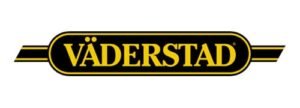
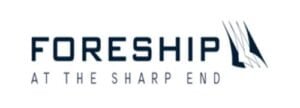
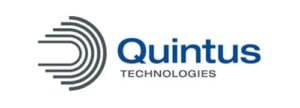
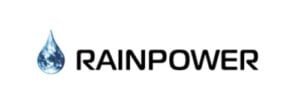
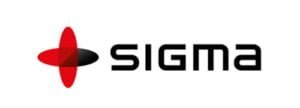

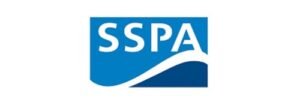
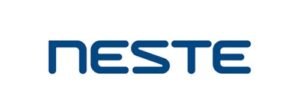
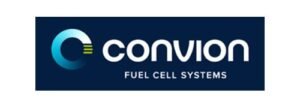
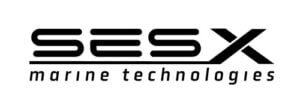
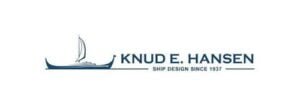
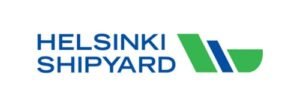
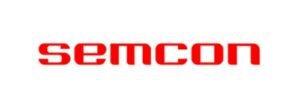
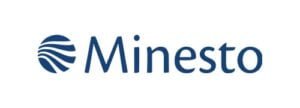
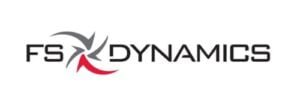
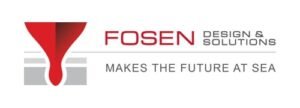
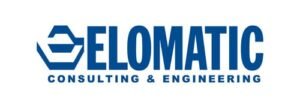
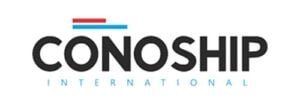
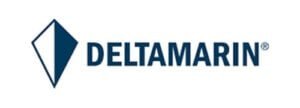
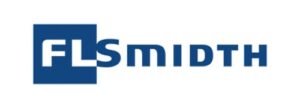
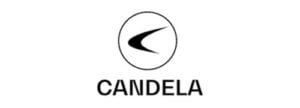
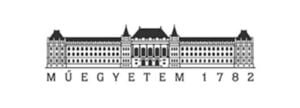
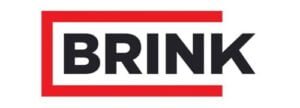
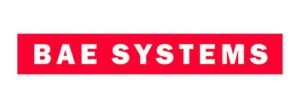
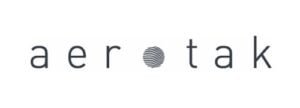
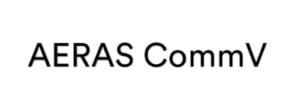
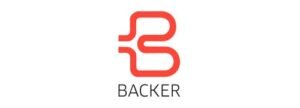
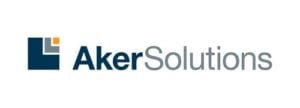
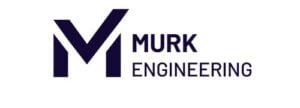
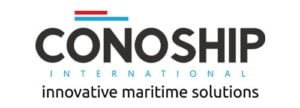
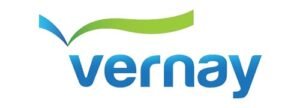
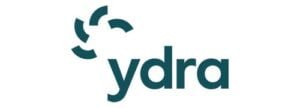
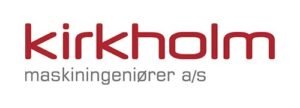
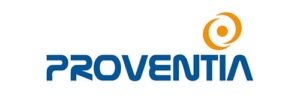
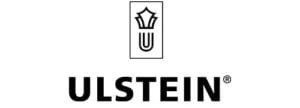
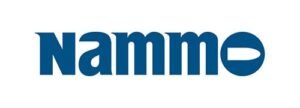
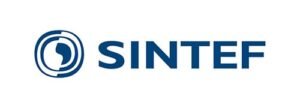
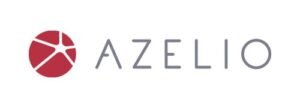
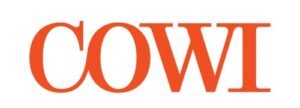
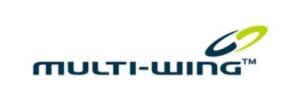
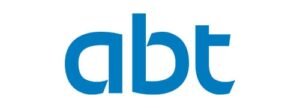
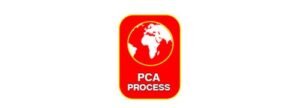
Volupes contacts for Simcenter FLOTHERM
Transient thermal analysis at its best
FLOTHERM provides robust capabilities for simulating transient thermal behavior in complete systems. Engineers can input time-dependent boundary conditions, such as varying heat sources, power dissipation profiles, or environmental conditions, to replicate real-world scenarios.
This software then solves the transient heat transfer equations, considering factors like conduction, convection, and radiation, to predict temperature distribution and heat dissipation patterns over time.
By performing transient thermal analysis, engineers can identify potential thermal design issues that might come up during different operational phases. This allows them to better optimize cooling strategies, identify critical hotspots, and evaluate thermal management solutions.
By accurately simulating and analyzing transient thermal behavior, engineers can make informed design decisions, ensuring the system operates within safe temperature limits and stays reliable.
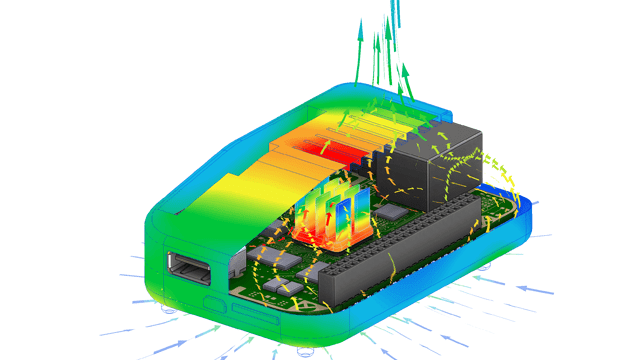
What can you do with FLOTHERM?
FLOTHERM is a powerful thermal analysis software that enables engineers to perform comprehensive simulations and explore a variety of thermal mitigation strategies.
Test design modifications quickly. Simply import the design, apply boundary conditions, and run simulations based on the defined boundary conditions and modified design. Predict airflow and heat transfer, run a transient analysis or parametric analysis, and gain power versus time data quickly.
Perform comprehensive thermal analyses. By importing the CAD geometry and defining boundary conditions, engineers can simulate heat transfer and fluid flow to predict temperature distribution, airflow patterns, and heat transfer.
Plus, create and assemble components of a thermal model to accurately represent the design you’re analyzing with a model assembly process that is straightforward, enabling engineers to run simulations with confidence.
FLOTHERM automatically creates a computational mesh and applies physics-based models to solve the governing equations. After running the simulations, engineers can analyze the results to identify hotspots, optimize cooling strategies, and make informed design decisions.
Visualize design improvements quickly. By visualizing design improvements in real-time, engineers can assess the impact of various modifications or optimizations. They can evaluate different cooling strategies, adjust parameters, or test alternative component placements to see how these changes affect the thermal performance of the system, enhancing the design process, fast.
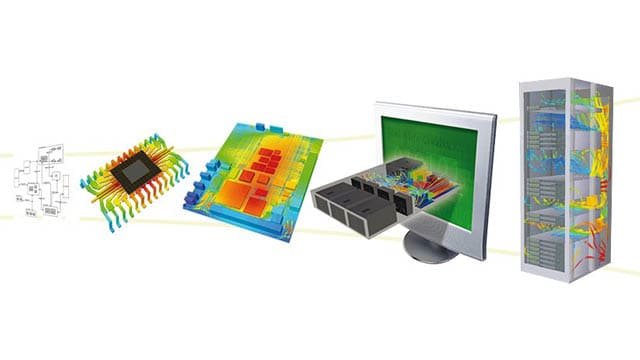
Key features and capabilities
Automatic sequential optimization. The automatic sequential optimization feature in FLOTHERM saves time and effort by eliminating the need for manual adjustments and iterations. Engineers can set constraints, such as temperature limits or airflow requirements, and let FLOTHERM systematically explore different design options to get to the right thermal performance.
During the optimization process, FLOTHERM intelligently adjusts the specified design parameters, evaluates the thermal behavior of each configuration, and compares the results against the optimization goals you’ve defined. It continues to refine and iterate through the design space until the best design configuration is identified.
Explore time-dependent power dissipation. Model a variety of different transient behaviors such as time-dependent power dissipation in components and transient thermostatic control modeling, where model input is varied as a function of monitored temperature.
Intelligent model creation macros. Streamline the process of creating accurate thermal models for complex designs. These macros are pre-programmed automation tools that intelligently generate models based on the design inputs the user provides.
Simcenter FLOTHERM electronics thermal analysis FAQs
What are the key benefits of using Simcenter FloTHERM for thermal analysis?
Simcenter FLOTHERM offers a range of benefits, including accurately predicting temperature distribution, identifying hotspots and potential thermal issues, optimizating cooling strategies, with reduced reliance on physical prototypes, faster design iterations, and improved overall thermal performance.
Can Simcenter FLOTHERM analyze both steady-state and transient thermal behavior?
Yes, Simcenter FloTHERM offers powerful transient analysis capabilities, analyzing both steady-state and transient thermal behavior. It can simulate temperature variations over time, capturing the dynamic response of the system to changing operating conditions.
How does Simcenter FLOTHERM handle complex geometries?
Simcenter FLOTHERM allows users to import or create detailed 3D models of their designs, including electronic components, enclosures, heat sinks, and more. This software utilizes automatic mesh generation and adaptive mesh refinement to accurately capture the geometry and ensure precise thermal analysis.
Can Simcenter FLOTHERM simulate different cooling strategies?
Yes, it supports the analysis of passive cooling methods such as heat sinks and thermal interface materials, as well as active cooling solutions like fans, liquid cooling systems, or heat exchangers. Engineers can compare and optimize different cooling options to get the right thermal performance.
Does Simcenter FLOTHERM have post-processing and visualization capabilities?
Yes. Engineers can analyze and visualize simulation results through temperature contours, airflow patterns, heat flux distribution, and other parameters. This enables a better understanding of thermal behavior and assists in identifying areas for improvement.
Can Simcenter FLOTHERM integrate with other engineering software tools?
Yes, Simcenter FloTHERM supports integration with other engineering software tools through standard data exchange formats. This facilitates seamless collaboration and enables engineers to leverage the capabilities of different software platforms for comprehensive design analysis and optimization. It can connect to PLM, CAD, simulation, and industrial IoT if your organization is in the process of digital transformation and integration.
Our Promise
Why Choose Volupe for Your CFD Needs?
Volupe is dedicated to offering top-tier CFD solutions. Our STAR-CCM+ software caters to various industries. It guarantees optimal results for engineers and analysts in fields like marine, automotive, aerospace, and energy.
Simcenter suite
Siemens Simcenter efficiently solves fluid flow problems. Optimize designs and analyze physics problems with advanced software. Reach engineering heights with Siemens Simcenter.
Get started
Start your CFD journey by exploring the process - get ahead today!
We care about support to our customers
Volupe has consistently been recognized as a top partner for customer support by Siemens Digital Industries Software. Our unwavering commitment to delivering exceptional service and support to our valued customers has been repeatedly acknowledged. These accolades serve as a testament to our dedication to providing the highest level of assistance and expertise in the industry and particulary STAR-CCM+
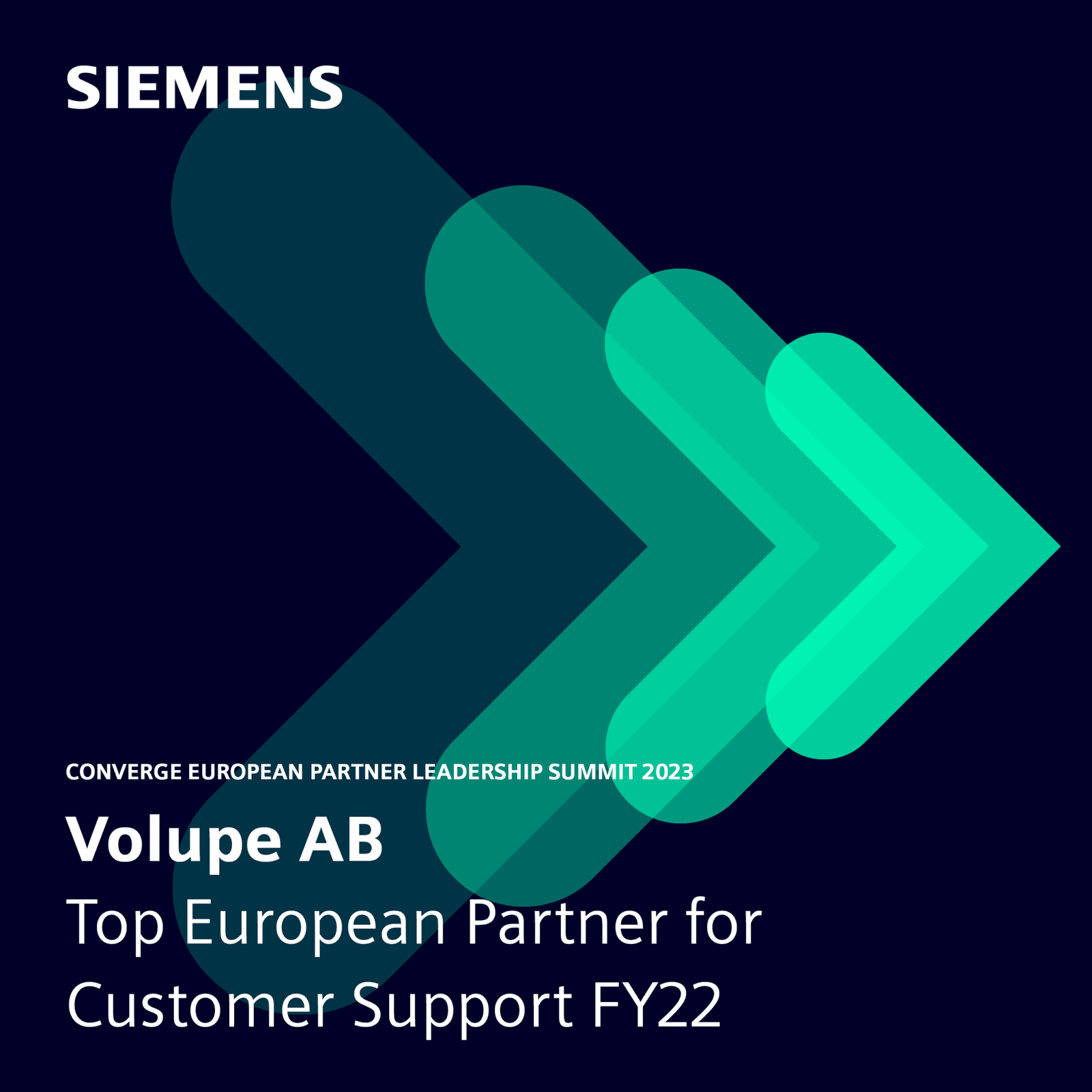
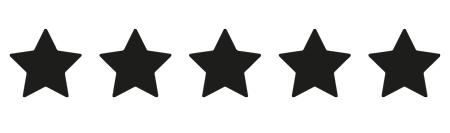
Customer success and Support
The Volupe customer success program includes regular technical follow-up meetings with our Customer Success Manager Carl Stenson. We go through what projects you have carried out, what you see in front of you and how we can support you in the best possible way. All our customers will be appointed a dedicated support technician who will be your first point of contact and carry relevant experience from your industry and how the software can be used efficiently and accurately.