With the possibility to simulate ship resistance and wake field, naval architects get access to detailed flow behavior. Yet, only together with self-propulsion simulation we can fully predict the powering performance of full-scale ships. We can predict the speed with which a ship hull moves through water in response to the thrust supplied by a spinning propeller, or determine which propeller speed is needed to balance resistance and thrust at a prescribed trail speed. Simcenter STAR-CCM+ provides a methodology by which you can predict the speeds:
- The simplest approach is to model the propeller as a momentum source in a cylindrical region representing the propeller disk, using a propulsion force.
- Virtual Disk: This model automatically generates a momentum source according to some geometric parameters and a propeller performance curve.
- If a higher fidelity simulation is necessary, the average effect of the propeller can be modeled using the Moving Reference Frame (MRF) approach.
- In order to take into account the full effect of the propeller, including the blade/rudder and blade/hull interactions, you can implement a rigid body rotation to the propeller disk region, as set up in the second approach.
The complexity and numerical effort are ascending in list above. For a general overview of Rotating Flow, please refer to Rotating Flow Part 2. We will for the implementation of self-propulsion for marine application focus on the Virtual Disk model. This Body Force Propeller method allows you to model the propeller and hull interaction without the added cost of modelling the propeller geometry with a fine mesh and smaller time scales.
This said, we will outline changes to the VTT template for self-propulsion in the following section and start by introducing a volumetric mesh refinement for the propeller plane and wake respectively. This is, however, not comparable with a mesh resolution needed for propeller geometry but it is necessary for resolving the extra acceleration of the flow field.
Add Refinement Geometry
We add a refinement box to the Bow and Stern refinement in 3D-CAD and use the same main dimension for parametrization (Bwl) factor dimensioning. A box-shaped refinement is best suited for fitting the structured mesh.
We will also add an option to prescribe an initial trim of the hull (not in the VTT template by Siemens). Which requires to extend all refinements (including Block for Underwaterhull) with maximum 1.3 times the draft.
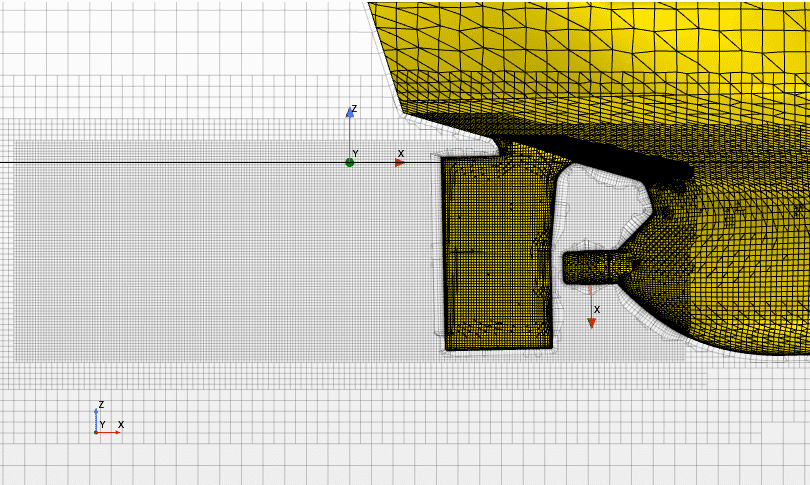
All added geometry will slip through the filter used in the VTT template. Thus the newly created box refinement need to be added to Tools > Filters > ImportedVesselPart as a static object:
To add the refinement we can simply copy the Stern0 refinement, rename it to Propeller0 and halve the Custom Size to 3.125% of base:
Add Initial Trim
To account for initial trim we can add a Rotation Transform to the Position Hull Operation. As the rotation reference we use a coordinate system (Midship) placed on mean draft and at ${Calculation Loa}/2 in x-direction.
Selecting Virtual Disk Model
For this simulation, we model the effects of the propeller on the ship using the body force propeller method. This method belongs to the virtual disk model.
Using the virtual disk for a propeller requires you to define the following items:
- dimensions and location of the disk
- orientation of the disk axis. This orientation defines the direction of the thrust force. (Initial trim needs to be included)
- propeller performance data, where the thrust coefficient KT and the torque coefficient KQ are provided as a function of advance ratio J
- velocity plane on which to obtain an average velocity and density for the inflow surface of the virtual disk
To set up the virtual disk model:
- Right-click the Continua > Physics VTT > Models > Select Models and add Virtual Disk
- Once the model is added, right click Continua > Physics VTT > Models >Virtual Disk > Virtual Disks node and select New.
- Edit the Virtual Disk node and set Method to Body Force Propeller Method.
Before you can specify the propeller curve, you must import the propeller table data file (here in .csv format) into Simcenter STAR-CCM+.
- Right-click Tools > Tables and select New Table > File Table.
- Navigate to your Openwater data sheet and click Open.
- Assign the table data to Propeller Curve node:
Positioning the Virtual Disk
Next, we need to position and dimension the virtual propeller. The recommendations to follow for the dimensioning of the Disk Geometry mentioned here and discussed be Siemens here. The analysis shows a change in thrust as the finite volume mesh is refined in the region around the virtual disk. The trimmer mesh produced similar results at 4 cells across the thickness of the disk.
Particularly the thickness of the Virtual disk has to be considered since the VTT template uses Multi-Mesh Sequencing which starts from a rather coarse mesh and the Virtual Disk might be too thin at the first mesh sequences. We therefore add a max() function to either include at least 3 cells across the propeller disk of 10% of the diameter.
For the positioning we add a new vector input parameter for the propeller plane position following the convention for naval architects as pictured above. Since the hull is positioned and Virtual disk needs to follow the ships coordinate system, moving through out the simulation, we need to calculated the final position of the propeller plane in two simulation operations. Here we also need to account for the rotation due to initial trim:
Calculation_Xprop_final = -(${LCG}-(-1*${Calculation Xmin}+$${Input_Prop_Pos}[0] ))-(tan(${Input_initialTrim})*(-(${Input T}-$${Input_Prop_Pos}[2] - tan(${Input_initialTrim}) * (${Calculation Loa}/2-(-1*${Calculation Xmin}+$${Input_Prop_Pos}[0] ))))) Calculation_Zprop_final = -(${Input T}-$${Input_Prop_Pos}[2]-tan(${Input_initialTrim})*(${Calculation Loa}/2-(-1*${Calculation Xmin}+$${Input_Prop_Pos}[0] )))
In the Disk Geometry > Normal And Coordinate System node, we also specify the connection to the ships coordinate system and account for initial trim of the propeller plane.
For the force balance we assume that the ship is supposed to operate at a fixed design speed (Input Vvessel in VTT template) and that the Virtual Disk model can adjust the propeller RPM to determine the operation point of the propeller. This means we need to balance the thrust with the current resistance of the ship by the following field function in the Virtual Disk > Thrust node:
${Time} < 2.5 * ${Convective Timescale} ? ${Resistance Total mean}/1/cos(${TotalPitch} - 0.0) * (${Time}/(2.5*${Convective Timescale})) :${Resistance Total mean}/1/cos(${TotalPitch}- 0.0)
With the Virtual Disk Model in place, we are now able to add post-processing for monitoring the action of the propeller. The Virtual Disk Model comes with various reports from which monitors and plots can be created, see picture below.
For more visualization we can create a scalar scene as described in a tutorial video by Siemens How can I visualise the velocity vectors on a propeller disk section which moves with a DFBI body?
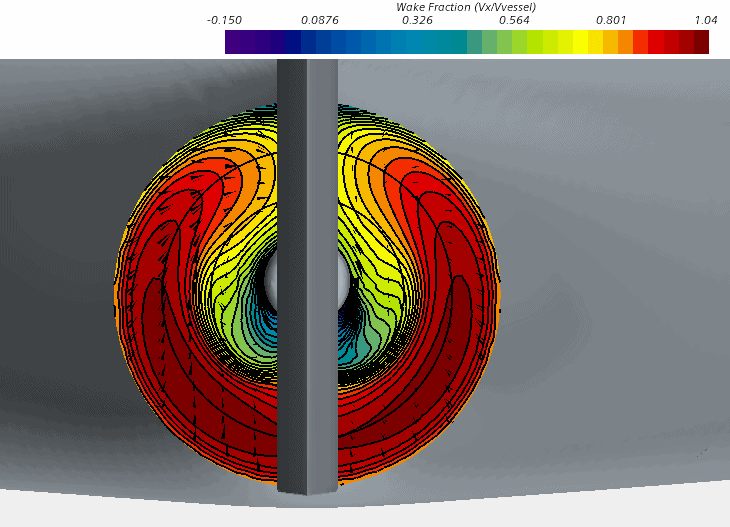
Test
To test the new self-propulsion template we use a well known hull geometry of the MV Regal with an arbitrary open water curve.
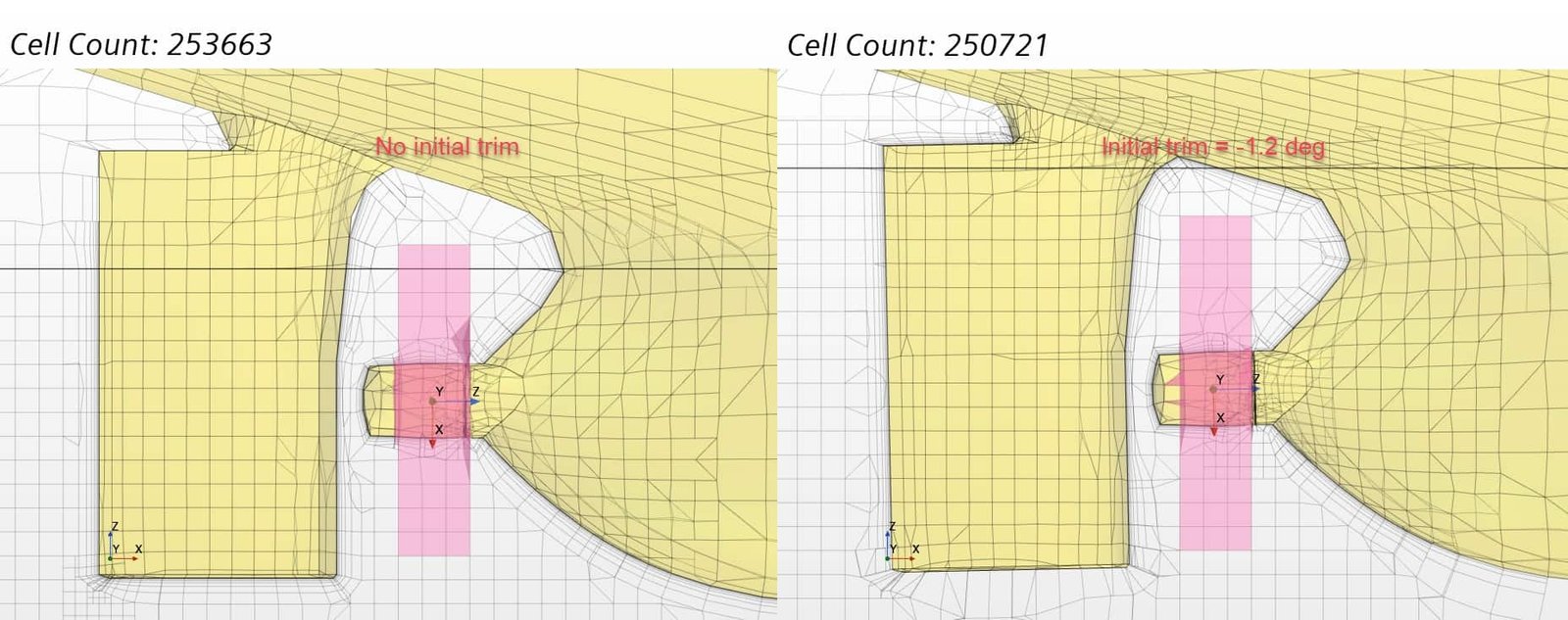
The positioning of the Virtual Disk is calculated with respect to an initial trim specified. And cells marked for Body Force action are selected depending on the mesh resolution.
With this modified version of VTT template, you can calculate the resistance of bare hulls as well as self-propelled. We hope the topic of this article is interesting and that you can use this to reach your goals with Simcenter STAR-CCM+ faster. Please find attached the implementation of a Self-Propulsioin template. And let us know if you have any questions or comments at support@volupe.com.
The Author
Florian Vesting, PhD
Contact: support@volupe.com
+46 768 51 23 46