Have you ever wondered how to set up propulsion units using the Virtual Disk model in Simcenter STAR-CCM+? Nozzle propellers, pod propellers, and Energy Saving Devices have made significant contributions to the advancement of marine propulsion technology. These designs offer improved efficiency, maneuverability, and control. It is no wonder that propulsion simulations can be beneficial for determining power consumption.
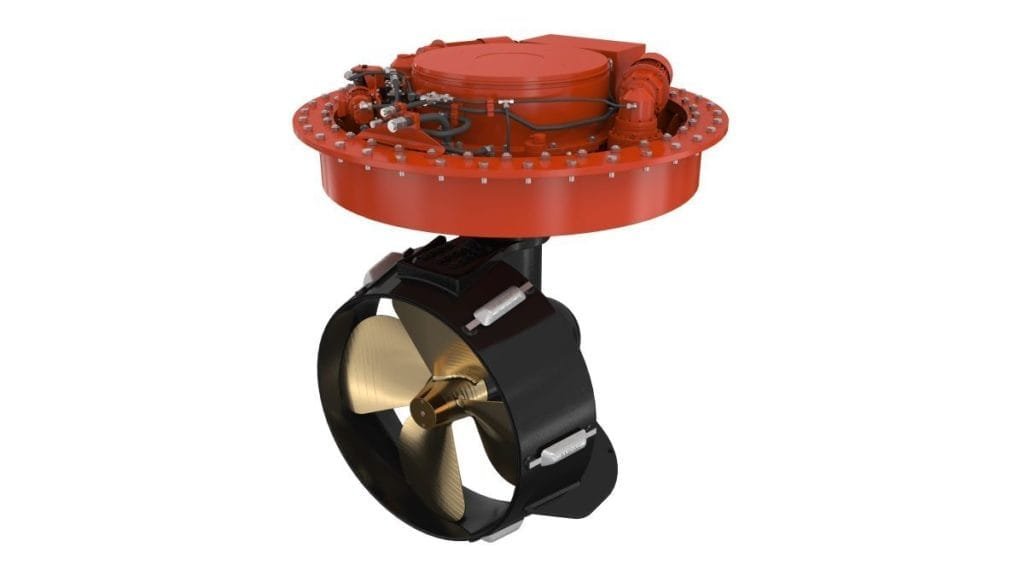
The Virtual Disk model in Simcenter Star-CCM+ is a physics model that effectively reduces computational costs by representing a propeller’s influence on fluid as momentum sources. In this week’s blog, we will explore the process of setting up a simulation for a ducted propeller of the ka-470 series.
The ka-470 propeller series data, including the generic nozzle 19A, is publicly available [1]. This data allows us to conduct generic tests to simulate a propeller operating in a confined environment using the Virtual Disk model. It is important to note that the most accurate representation would involve modeling the rotating propeller geometry.
The question arises regarding the most accurate representation of the unit. We have two options: we can model the duct, pod, and auxiliary geometry with the Virtual Disk inside. In this case, we apply the open water performance of the propeller to the Virtual Disk. Alternatively, we can model only the pod and incorporate the effect of the nozzle into the open water input data for the Virtual Disk model.
To validate the setup of our ducted propeller, we can refer to the open water diagram from literature. Although the mesh may not be ideal for the entire range of advance ratios, it provides satisfactory thrust coefficients in the low range of J values, such that we can then perform our two simulations using the Virtual Disk model. However, before that, we need to create an open water curve of the propeller using the MRF (Multiple Reference Frame) approach in Simcenter STAR-CCM+.
Virtual Disk with Total Open Water
For the first approach we need the open water curve of the unit from the literature as input to the Virtual Disk. However, it should be noted that this approach is not entirely accurate since the thrust component from the duct will be applied uniformly across the entire disk. The geometry representation within the domain, including only the propeller shaft as shown above.
Simulating the range of J values in an open water setup shows that we get a performance offset that is about 25% lower than the input data. Yet the KT-curve follows the curvature of the open water data from the series.
Virtual Disk inside nozzle
In the case of the Virtual Disk located inside the duct, we utilize open water data obtained by simulating the open propeller using the MRF method in Simcenter STAR-CCM+. It is worth noting that the thrust coefficient for the open propeller is lower compared to the KT tot of the unit. As a result, the generated thrust from the Virtual Disk is also lower, although it receives an additional uplift from the duct geometry.
However, upon examining the open water diagram provided above, it is evident that the total thrust produced by both the Virtual Disk and the duct is even lower than the total thrust generated by the Virtual Disk alone with complete open water data.
Summary and recommendations
The results of both simulations show that the Virtual Disk is not able to reproduce the open water data of their input data. Although following the guidelines for the definition of the Virtual disk and inflow plane in terms of discretisation.
The approach of modelling the Virtual Disk with the input of the total ducted propeller unit represents better performance in terms of thrust generation. But the flow field is significantly simplified as shown below. Representing the duct geometry allows to develop the wake as shown below, comparing the pure Virtual Disk, Virtual Disk with duct geometry and MRF with propeller and duct representation.
In summary, the Virtual Disk model is a computationally efficient way to simulate the influence of propellers on fluid flow without directly modelling the geometry itself. This offers a great opportunity to simulate self-propulsion operation point with minimal computational effort, while cutting some of the propeller performance. The Virtual Disk can be place in a confined space and will help to develop the flow field correctly. However, when is comes to the thrust accuracy, the best approach is to provide the Virtual Disk with open water data from the ducted propeller unit.
As the maritime industry continues to evolve, further research and development in propulsion units like nozzle propellers and pod propellers are expected to drive innovation and shape the future of marine transportation. We hope you find this investigation use full for your next self-propulsion simulation. As always, please do not hesitate to contact us at support@volupe.com if you have any questions or comments.
[1] OOSTERVELD, Marinus Willem Cornelis. Wake adapted ducted propellers. 1970.
The Author
Florian Vesting, PhD
Contact: support@volupe.com
+46 768 51 23 46