Design Reuse supports the iterative workflow of Computational Fluid Dynamics by reusing information from previous runs on a new design alternative, allowing us to start a new design study with an initialization that’s already closer to an expected solution, saving valuable time and computational resources.
What is Design Reuse?
Design Reuse is an innovative feature within STAR-CCM+’s Design Manager allowing new designs to start closer to the expected results. Instead of initializing each design study from scratch, Design Reuse leverages results from previous successful designs, specifically selecting the closest one in the parameter space
How Design Reuse Works in STAR-CCM+
The Design Reuse feature in STAR-CCM+ operates by examining the parameter space of completed designs and using results from the one closest to the new design’s input values. By identifying and reusing data from previously successful designs, Design Reuse reduces the need to calculate each design from scratch, saving time and computational resources.
Activation Conditions
Design Reuse is available for four types of design studies:
- Sweep
- Design of Experiments (DOE)
- Adaptive Sampling
- Optimization
It is important to note that this feature is not applicable in studies using Surrogates as the Evaluation Method. If a study is configured to use Surrogates, Design Reuse will remain inactive, ensuring compatibility only with studies that involve direct calculations.
Calculating Parameter Distance
To determine which past design to reuse, Design Manager evaluates the distance between the new design’s input parameters and those of previously successful designs. This distance is calculated in the parameter space using a Euclidean Distance formula that considers the values of all input parameters, such as length and chord size in an aerodynamic study.
D_{max}=\sqrt{(p_{1,max}-p_{1,min})^2+(p_{2,max}-p_{2,min})^2+(p_{3,max}-p_{3,min})^2+…}
Once calculated, the distance is normalized using the Global Maximum Distance—the Euclidean Distance between the minimum and maximum possible values of all input parameters. This normalization process allows Design Manager to compare distances in a standardized way, regardless of the scale of individual parameters.
Threshold-Based Initialization
The decision to reuse a design is based on a Maximum Normalized Distance threshold, which can be set by the user. If the normalized distance between the new design and an existing one is below this threshold, Design Manager will reuse the result from the closest design to initialize the new one. By default, this threshold is set to 0.3, which allows reusing designs that are within 30% of the maximum possible distance. However, users can adjust this threshold as needed:
- Setting it to 0 effectively disables Design Reuse, as no previous designs will meet the threshold.
- Setting it to 1 allows the reuse of any available design, maximizing the likelihood of reusing results but potentially sacrificing design novelty.
Tie-Breaking in Design Reuse
In cases where more than one successful design has the same normalized parameter distance to the new design, STAR-CCM+ defaults to reusing the design with the larger design number. This tie-breaking mechanism ensures a consistent, automated approach to selecting between equally suitable designs.
Through these mechanisms, Design Reuse optimizes initialization by setting each new design study closer to a likely solution, contributing to faster and more effective workflows. For users, the ability to customize the threshold value means they can balance the reuse of previous designs with the need for novel calculations in high-sensitivity studies.

Example 1: Design Exploration of the Exhaust manifold
To better understand how the Reuse works in STAR-CCM+, let’s walk through an example. Imagine you’re running a design space exploration study to the pressure drop in an industrial exhaust manifold in connection with the outflow velocity uniformity. The study has a hand full of design parameters for a deflection plate. To explore the design space, we run Design of Experiment study with the Latin Hypercube Sampling.
In a traditional setup, each new configuration would restart the reference simulation, with all new design parameters. However, with Design Reuse activated, Design Manager scans previous designs to find the one with the closest combination of parameter to the new configuration. If this closest design falls within the specified distance threshold, its results are reused to initialize the new design study. Hence, we can get two new types of variants in separate design sets:
- Reused variants, which are became the starting point for a new design
- Reusing variants, which not started from the reference simulation
This process allows for an efficient initialization, with the new study beginning from a design configuration that’s already close to a likely solution. To track the reuse process, users can investigate the Design Details to view the origin of specific variants and see which designs are related to each other. This connection between designs provides transparency and insight into how each configuration builds upon previous results.
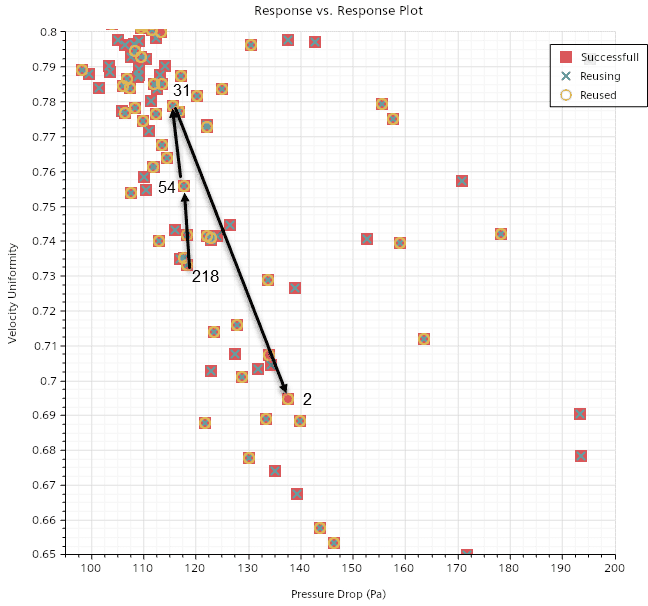
One key benefit of Reuse is its impact on overall study runtime. In this example, activating Design Reuse resulted in a 47% reduction in total runtime. This faster convergence, however, requires careful consideration of stopping criteria. It’s essential to set appropriate stopping points, such as monitor-based stopping criteria or a fixed number of iterations, to prevent premature convergence when reusing designs. Alternatively, users can enable the “Clear History” option to reset the solution history for each design, ensuring that reused designs undergo thorough recalculations.

Conclusion
The Design Reuse feature in STAR-CCM+ Design Manager is a game-changer for us looking to optimize simulation studies efficiently. By reusing results from similar, successful designs, this feature reduces simulation time, saves computational resources, and enables a seamless, automated workflow. Whether used in complex industrial studies or multi-parameter explorations, Reuse helps achieve quicker, high-quality results with minimal manual setup. Let´s reuse your simulation and find out how much time you can save support@volupe.com!
The Author
Florian Vesting, PhD
Contact: support@volupe.com
+46 768 51 23 46