DFBI Equilibrium Core Concept
The equilibrium body motion option seeks to balance forces and moments on a 3D rigid body across specified degrees of freedom (up to six). The numerical procedure assumes a steady-state condition where forces and moments in the selected directions (translation or rotation) converge to zero. Unlike dynamic motion, this method is mathematical rather than physical, aiming for computational efficiency while preserving accuracy.
Numerical Procedure
The numerical procedure for finding the equilibrium position operates iteratively:
- Step Size Calculation: At each time-step, Simcenter STAR-CCM+ calculates a step size for translation and rotation.
- Body Movement: The rigid body moves incrementally based on the calculated step size. The flow must then adapt to this change in position.
- Force Convergence: Inner time-steps adapt the fluid flow around the body and resolve forces and moments until the Force and Moment Tolerance criterion is met or the Maximum Inner Time-Steps limit is reached. (Inner time-steps are regular time-steps. They are called inner time-steps because they apply between incremental movements of the body).
- Iteration: The process repeats until the forces and moments are balanced
Key Applications
- Sink and Trim Simulations: Determine the equilibrium orientation of a ship in water.
- Force Balancing: Analyze static equilibrium under combined fluid and external forces.
Control Parameters and Their Roles
The performance of the equilibrium body motion relies on several control parameters. Some of which are provided in absolute values which makes it difficult to use the defaults for ships varying size. We investigated these control parameters in an optimization study to meet the results of the free body motion while achieving better convergence.
Equilibrium Motion control:
1. Maximum Inner Time-Steps
Defines the maximum number of inner steps for force convergence before the next motion step.
Impact: Higher values increase convergence accuracy but extend computation time.
Optimization Insight:
- Larger vessels with complex hydrodynamic interactions may require more inner time-steps for stability.
- Prolonged inner time-steps reduce the risk of overshooting the motion (particularly heave converges faster with more inner time-steps)
2. Maximum Translation Step
Caps the linear displacement of the rigid body in each motion step.
Impact: Prevents excessive movements that could destabilize the solution or overshoot equilibrium.
Optimization Insight: Optimal values are proportional to the ship’s length. But a guideline is to relate the maximum also to the draft. Our recommendation is
Max Translation Step=frac{T}{2L_{WL}}
3. Maximum Rotation Step
Limits the angular displacement of the rigid body in each motion step.
Impact: Prevents abrupt rotational changes, maintaining solver stability.
Optimization Insight: Typically set relative to the vessel’s beam and draft. Values of 1% of the draft T are recommended
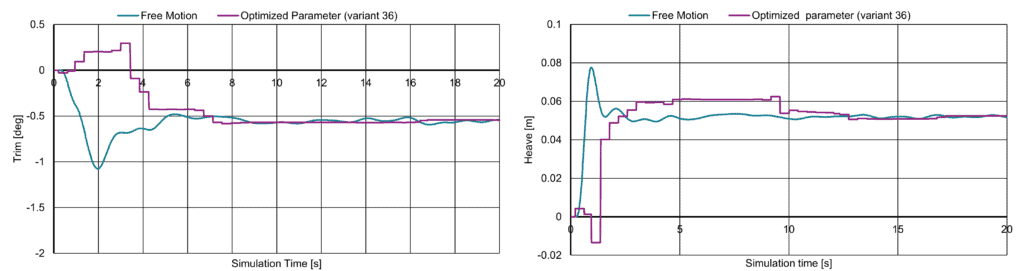
4. Under-Relaxation Factors (URF)
Applies a damping effect to translation and rotation motions.
Impact: Lower values improve stability but slows down convergence.
Use Case: Reduce URF values for complex geometries or simulations prone to divergence.
5. Growth Rate Controls
Maximum Translation Growth Rate: Limits the incremental increase of translation steps between inner steps.
Maximum Rotation Growth Rate: Restricts the growth of rotational steps.
Impact: Ensures smooth progression toward equilibrium, avoiding instability from abrupt changes.
Conclusion
The equilibrium body motion option in Simcenter STAR-CCM+ is a powerful tool for quasi steady-state DFBI simulations, offering efficiency and flexibility for maritime applications. Optimizing parameters like Maximum Inner Time-Steps, Translation Step, and Rotation Step is critical to balancing computational cost and solution accuracy. By scaling these parameters to vessel dimensions and leveraging convergence monitoring tools, practitioners can streamline simulation workflows and achieve reliable results.
The generic step size formulation can be incorporated into your simulation template for calm water resistance calculations. Applying the optimized values to the Kriso Container Ship (KCS) resistance test case demonstrates improved simulation performance, with enhanced motion convergence and minimized overshoot.
Have you encountered unique challenges in DFBI equilibrium simulations? Feel free to contact us at support@volupe.com
The Author
Florian Vesting, PhD
Contact: support@volupe.com
+46 768 51 23 46