Empirical correlations for convective heat transfer coefficients
As a CFD engineer it is not uncommon that you encounter a problem where you need to know the convective heat transfer coefficient.
It could be a case where you need to take into account the effects of a heating/cooling flow as a boundary condition, or perhaps a case where you would like to validate (or at least make a sanity check of) your simulation results. To help you in your daily work, we decided to summarize the most commonly used empirical correlations for estimating convective heat transfer coefficients in the sections below.
The correlations are given in terms of Nusselt number, Nu, which is a dimensionless property stating the relation between convective heat transfer and conductive heat transfer within a fluid. To help you even further, we have also created a Nusselt number calculator, incorporating all correlations listed on this page.
The Nusselt number definition reads
Nu = \cfrac{hL}{k} (1)
where h is the convective heat transfer coefficient, L is a characteristic length and k is the thermal conductivity of the fluid. Many generalized applications give correlations for the average Nusselt number, \overline{Nu}, but some applications also allow for estimation of the local Nusselt number (i.e. based on coordinate or position on a given geometry). The average Nusselt number is defined similar to Equation 1 by simply replacing the local heat transfer coefficient, h, with the average heat transfer coefficient, \overline{h}.
Other dimensionless quantities needed as input to the correlations are typically the Reynolds number, Re, Prandtl number, Pr, Rayleigh number, Ra and Grashof number, Gr. You can read up on some of these quantities here: Dimensionless numbers – VOLUPE Software.
Quick access links
Click any of these links to navigate to your correlation of interest:
Correlations for natural convection
The following correlations have been derived for purely buoyancy driven flows (i.e. natural or free convection) and for such circumstances the Nusselt number is typically expressed as a function of Rayleigh number and Prandtl number, i.e.
Nu = f\left(Ra, Pr\right) (2)
The Rayleigh number is defined as the product of the Grashof number and the Prandtl number, Ra = Gr Pr. The Grashof number is a quantity describing the relation between buoyant and viscous forces acting on a fluid, defined as
Gr_x = \cfrac{g\beta\left(T_s-T_{\infty}\right)x^3}{\nu^2} (3)
where g is gravitational acceleration, \beta is the coefficient of thermal expansion, T_s is the surface temperature, T_\infty is the bulk temperature, x is the characteristic length and \nu is the kinematic viscosity. The Prandtl number describes the relation between momentum diffusivity and thermal diffusivity and is defined as
Pr = \cfrac{\nu}{\alpha}=\cfrac{c_p\mu}{k} (4)
where \alpha = k/\left(\rho c_p\right) is the thermal diffusivity and \mu is the dynamic viscosity. To summarize, the Rayleigh number can be thought of as an indicator of occurence of natural convection, as it relates thermal transport through diffusion to thermal transport through convection. Below a critical value of Ra there is no flow and heat is transferred purely by conduction. Above this critical value natural convection is dominating the heat transfer. In most engineering problems the critical point is somewhere between 10^6 and 10^8.
Natural convection on a vertical surface
Figure 1: Natural convection boundary layer development on a vertical surface.
Natural convection on an inclined surface
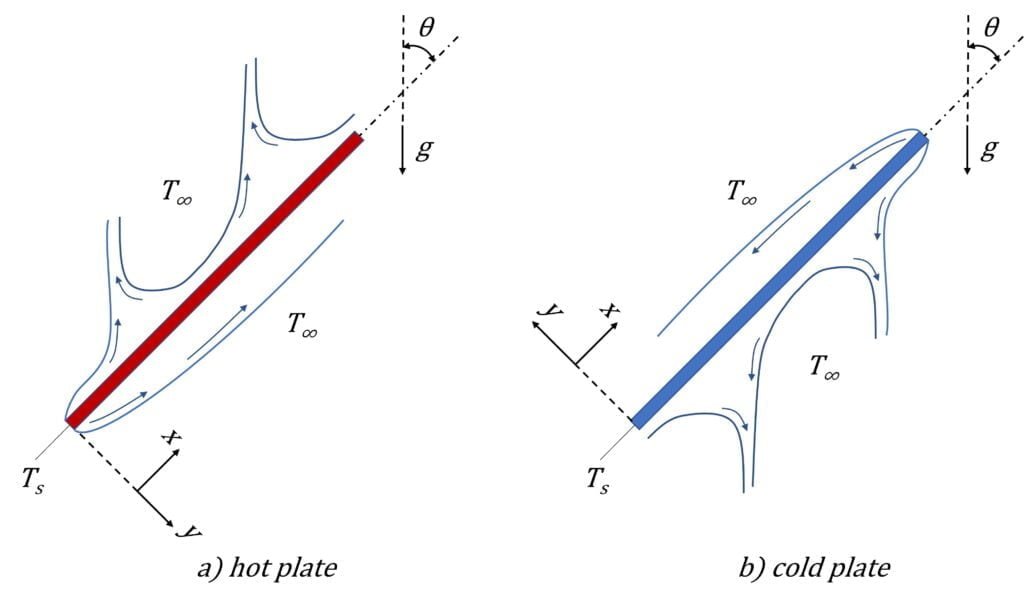
Natural convection on a horizontal surface
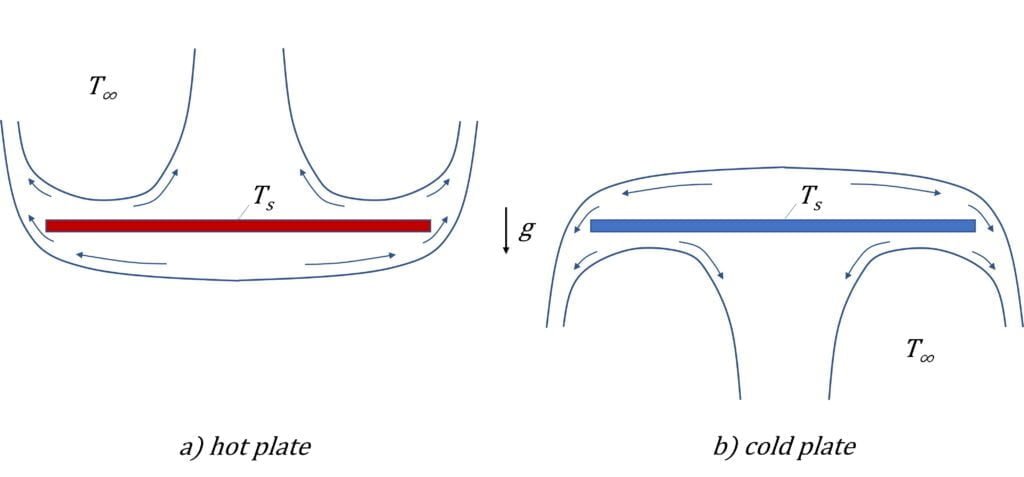
\overline{Nu}_L=0.27 Ra_L^{1/4} \left(10^5 \lesssim Ra_L \lesssim 10^{10} \right) (9)
Note that the best accuracy is achieved by redefining the characteristic length as
L=\cfrac{A_s}{P} (10)
where A_s is the surface area and P is the surface perimeter.
Natural convection on a (long) horizontal cylinder
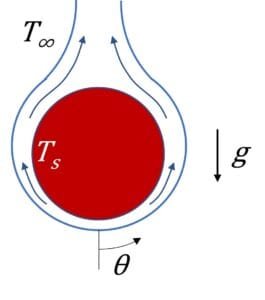
Correlations for forced convection
Nu = f\left( Re, Pr \right) (12)
Forced convection on a flat plate in parallel flow
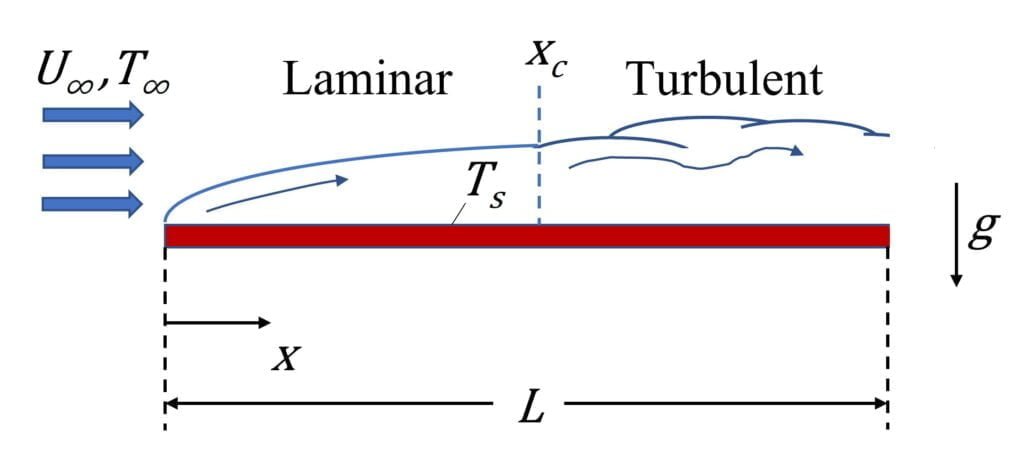
Nu_x = 0.332Re_x^{1/2}Pr^{1/3} Pr \gtrsim 0.6 (13)
For the same conditions, it also follows that the average Nusselt number at a point x \le x_c is twice the local Nusselt number, i.e.
\overline{Nu}_x = 2 \cdot Nu_x = 0.664Re_x^{1/2}Pr^{1/3} Pr \gtrsim 0.6 (14)
Assuming instead that the flow has transitioned into the turbulent regime, the local Nusselt number can be expressed as
Nu_x = 0.0296Re_x^{4/5}Pr^{1/3} 0.6 < Pr < 60 (15)
Moreover, the average Nusselt number in the case where there are mixed (i.e. both laminar and turbulent) boundary layer conditions can be approximated by
where Re_{x,c} is the critical Reynolds number where transition occurs. In a situation where L \gg x_c the laminar contribution becomes negligible and Equation 16 can be simplified to
\overline{Nu}_x = 0.037Re_x^{4/5}Pr^{1/3} (17)
Neglecting the laminar contribution, Equation 17 is hence also an appropriate approximation for a case where there is a turbulent boundary layer across the entire plate.
Considering instead a situation where there is a uniform surface heat flux, the local Nusselt number for a laminar flow can be approximated by
Nu_x = 0.453Re_x^{1/2}Pr^{1/3} Pr \gtrsim 0.6 (18)
The average Nusselt number across the entire plate can be found using the following expression:
\overline{Nu}_x = 0.68Re_x^{1/2}Pr^{1/3} (20)
Forced convection on a cylinder in cross flow
Another common forced convection application is the single cylinder in cross flow (see Figure 6 below).
Figure 6: Streamlines and wake formation around a long cylinder in cross flow.
Churchill and Bernstein have proposed a correlation for the average Nusselt number claimed to cover a wide range of Re_D and a wide range of Pr. This correlation is deemed valid for Re_D Pr > 0.2 and reads
\overline{Nu}_D=0.3 + \cfrac{0.62 Re_D^{1/2}Pr^{1/3}}{[1 + (0.4/Pr)^{2/3}]^{1/4}} \left[ 1 + \left( \cfrac{Re_D}{282 000} \right) ^{5/8} \right]^{4/5} (21)
\overline{Nu}_D = C Re_D^{m}Pr^{1/3} (22)
Suggested values for C and m are found in Table 1 below. Note that all properties used in Equation 22 should be evaluated at the so-called film temperature, i.e. T_f=(T_s+T_\infty)/2.
Table 1: Constants for Equation 22.
Forced convection on a bundle of tubes in cross flow
Many heat transfer applications in industry involves the flow around bundles of tubes, such as tube coolers or heat coils in boilers. The tube arrangements in such applications may vary, but typically they are either a) aligned or b) staggered. Schematic pictures of such arrangements can be seen in Figure 7.
Figure 7: Cross flow on different tube bundle formations.
Typically, the heat transfer coefficient on the first row of tubes (normal to the flow direction) is similar to a single cylinder in cross flow. The further we move into the bundle the heat transfer coefficient tends to increase until it usually stabilizes after four or five rows of tubes. For a bundle of ten or more rows of tubes (N_L \ge 10), Grimison has proposed a correlation for airflow. To account for other types of fluids, his correlation is usually extended with a correction factor based on Pr, giving the expression
\overline{Nu}_D = 1.13 C_1 Re_{D,max}^{m}Pr^{1/3} (23)
which is deemed valid for the following conditions
\begin{cases}N_L\ge10 \\ 2000<Re_{D,max}<40000 \\ Pr\ge0.7\end{cases}
U_{max} = \cfrac{S_T}{S_T-D}U_\infty (24)
U_{max} = \cfrac{S_T}{2(S_D-D)}U_\infty (25)
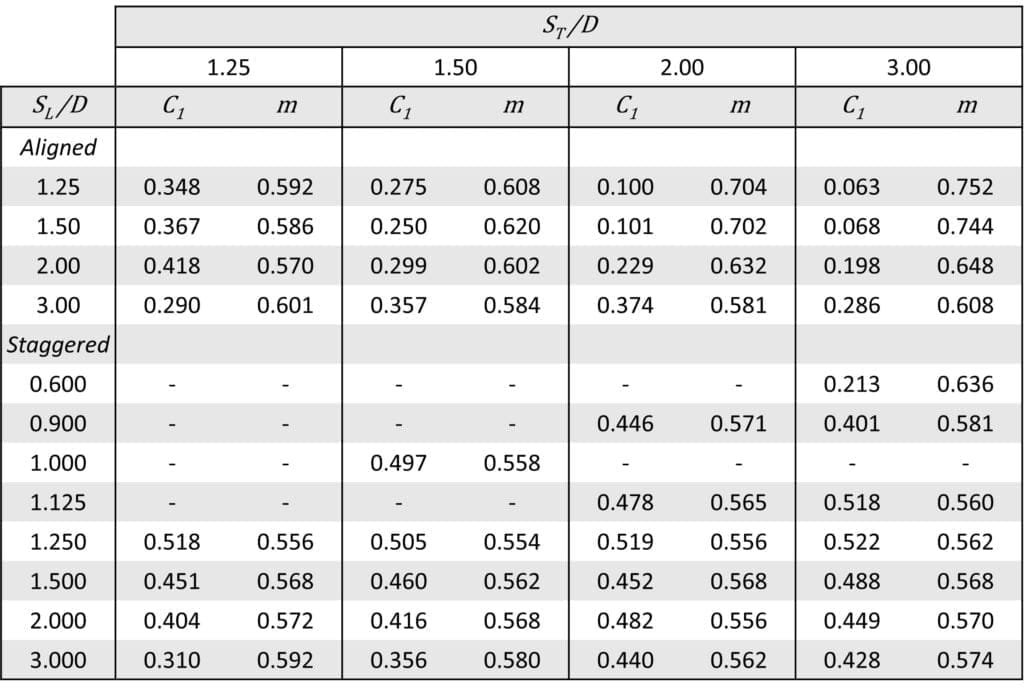

Forced convection in a circular tube
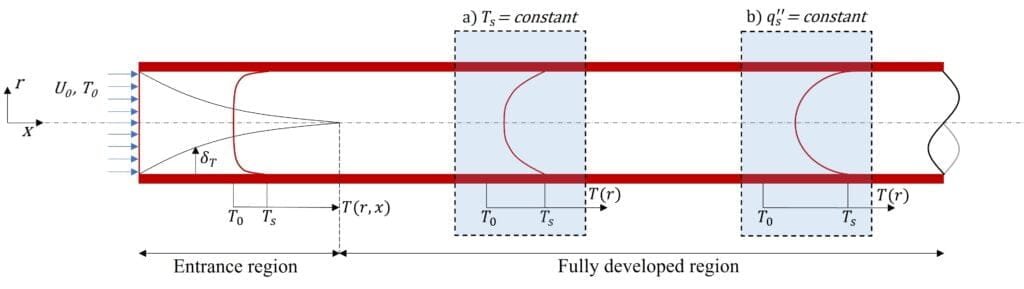
Forced convection in a non-circular duct
For turbulent flows, the correlations presented for circular tubes above may be applied also for ducts with non-circular cross sections by exchanging the tube diameter with the so-called hydraulic diameter in the calculations of the different parameters. The hydraulic diameter is defined as
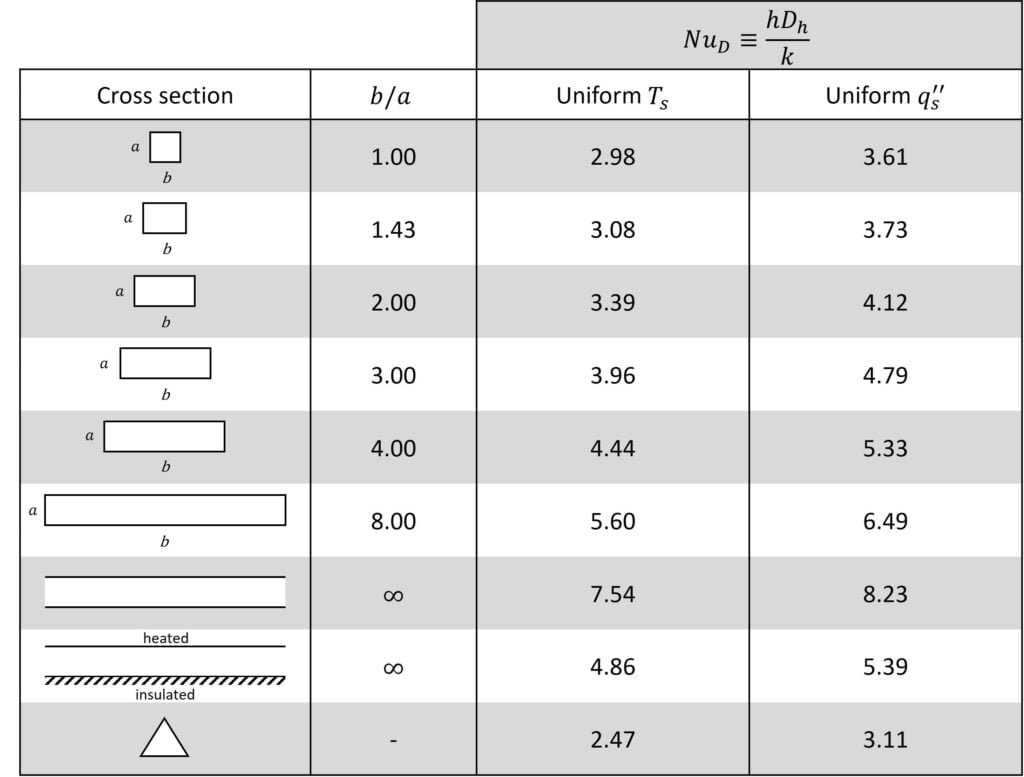
Final remarks
As aforementioned, the correlations listed above are merely a selection of what can be found in the literature. For further details or alternative correlations, the reader is therefore advised to approach the available literature.
Reference list
[1] Fundamentals of Heat and Mass Transfer (5th edition), Frank P. Incropera & David P. DeWitt, 2002, USA
[2] A Heat Transfer Textbook (5th edition), John H. Lienhard IV & John H. Lienhard V, 2020, USA (A Heat Transfer Textbook, 5th edition (mit.edu))
[3] Nusselt number, Wikipedia, Accessed February 2023 (Nusselt number – Wikipedia)
Author
Johan Bernander, M.Sc.
Application Specialist
Training and mentoring for the products in the Simcenter Suit
Volupe offers training and mentoring for Simcenter products, including an introductory course for Simcenter STAR-CCM+ with basic CFD concepts. Videos on fluid dynamics and CFD are also available for users without a background in the field.
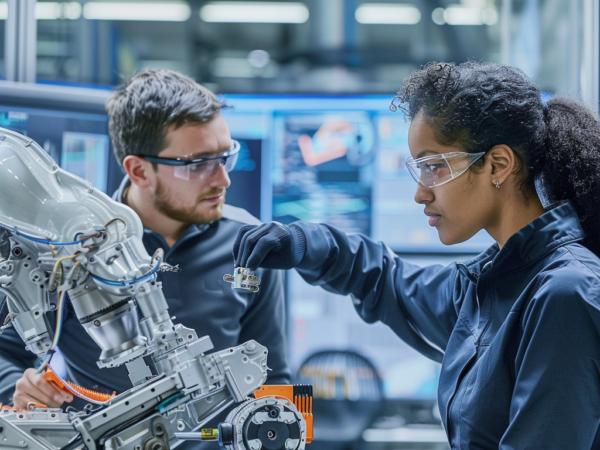